Specialized in Object and Library & Archive Conservation
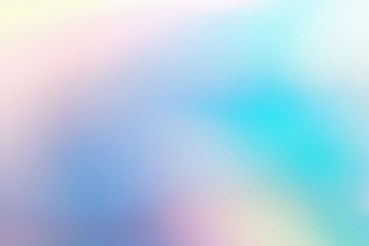
Siapo
Report Summary
Owner: Winterthur/ University of Delaware Program in Art Conservation; gift of The Baltimore Museum of rArt
Accession #: GACP1754d
Object: Siapo (barkcloth)
Maker/Provenance: Samoan (est.)
Object Date: 19th century (est.)
Materials: Mulberry fiber, natural dyes
Dimensions: 38 9/16" x 81 9/16" (98 x 207.2 cm)
Consulted:
Lara Kaplan, Objects Conservator and Affiliated Assistant Professor, Winterthur Museum, Garden & Library and the University of Delaware
Joan Irving, Paper Conservator and Affiliated Associate Professor, Winterthur Museum, Garden & Library and the University of Delaware
Laura Mina, Associate Textile Conservator and Affiliated Assistant Professor, Winterthur Museum, Garden & Library and the University of Delaware
Michele Austin-Denehy, Contract Conservator, National Museum of the American Indian
Dr. Adrienne Kaeppler, Curator of Oceanic Ethnography, National Museum of Natural History
Reggie Meredith Fitiao, Faculty in the Fine Arts Department, American Samoa Community College
Report Date: 03.05.2021
This was a collaborative treatment project between WUDPAC c/o 2022 students studying object conservation: Nylah Byrd, Bellie Camp, Allison Kelley, and Abby Rodriguez
Treatment Images
Historical Context
Siapo making is an art form passed down through generations, and a symbol of Samoan culture. These cloths can be used for clothing, ceremonial garments, burial shrouds, given as gifts, and more. The siapo is meant to be used up over time. Larger pieces of cloth are often cut into pieces, distributed, and repurposed until they can no longer be used, and even then the remnants may be recycled into a new cloth, or recycled for other purposes. The designs on the siapo are usually geometric in style, however there are cloths with a variety of animal themes designs. This particular siapo contains two design elements: ‘ali’ao and tuseli’l. ‘Ali’ao is a triangular pattern representing a trochus shell, which is a Samoan delicacy. Tuseli’l are small lines that represent a house broom or a hair comb.
Women tend to be the weavers of fine mats and barkcloths in Samoan culture, and they keep track of how many cloths and mats are in the household. The cloths in context are stored folded between other mats or bed mattresses. The movement from someone sleeping on the mattress on top of the siapo helps reduce wrinkles in the cloth. They are aired out periodically on sunny days, usually by laying them on a large relatively flat surface. After being aired out, the siapo is folded in a different way than it was previously so the creases do not become permanent. Keeping the siapo soft and supple is important as it has to maintain its flexibility to be wrapped around bodies and objects while maintaining movement. As noted above, this particular siapo is thought to be a lavalava or wrap-around skirt due to its size. These skirts can be worn as everyday clothing and during ceremony.
Materials and Technology
The production of siapo in Samaon communities begins with the harvest of the paper mulberry plant (Broussonetia papyrifera), or u’a. The u’a is grown specifically for use in siapo making. To remove the bark, a cut is made using a sharp implement such as a knife or even the siapo maker’s teeth. Once the cut is made, the bark and the inner bast fiber will separate readily from the wooden core. Once the bark is removed the strip is wrapped around the maker’s hand with the bast facing out to help flatten the strip. The outer bark is removed by once again using a sharp implement to separate the bark from the bast, then the bark is peeled away by hand down the length of the strip. The strips are then put into water to soak, allowing the fibers to hydrate and soften.
After soaking, sometimes for as little as five minutes, the strips are taken out of the water and spread flat onto an upright wooden board. The serrated edge of a shell is used to scrape away any remnants of the outer bark and to begin spreading the fibers apart. The whole strip is worked in this way, keeping it wet the entire time. Once fully cleaned, the strip is rinsed, folded, and pressed against the board with a smooth-edged shell to remove the excess water. The strips are then beaten against a wooden anvil, called a tutua. The beaters, called i’e, are rectangular and wooden, and they can have smooth or grooved faces, sometimes both on the same beater. Once the desired width has been achieved, the cloth is pulled taut to its full width and laid flat. Rocks are placed along the edges to allow it to fully dry in the desired orientation.
Once dried, the u’a is ready for joining and decoration. If the decoration is going to be applied using an ‘upeti, or rubbing board, the sections are joined as the pattern is applied (Figure 6). Siapo is often two-ply, with the two layers having opposite grain directions to confer strength to the overall cloth. The pieces are joined using a starch paste from the arrowroot plant. To join pieces of u’a, a cut edge of the tuber is rubbed directly onto the surface, depositing a layer of starch paste, and the piece to be joined is placed on top. This process is repeated as many times as needed to achieve the final dimensions of the siapo.
There are two primary methods of decoration, mamanu, or hand applied, and ‘elei or tasima, or the rubbing method. Both techniques use natural dyes as the primary colorant. The most prevalent color is a dark brown dye called o’a which darkens rather quickly with time and has a glossy finish. Other colors are a yellow (ago) from turmeric, a black (lama) made by adding the soot from roasted candlenuts to the o’a dye, and a red (loa) made from the pods of a “lipstick tree”. Dyes are applied with a brush called a paogo made from dried pandanus fruits. For the mamanu decoration, the patterns created with the dyes are applied by hand alone. In the rubbing method, a pattern board is used to define the overall design. The u’a is laid onto the board and a layer of red clay called ele is rubbed into the surface to emphasize the pattern and transfer it to the u’a. This siapo was likely produced using the ‘elei method with an ‘upeti that was stitched rather than carved. The stitched ‘upeti was made by sewing coconut midrib and bamboo strips onto a rectangle of pandanus leaves. The stitched supports were much more time consuming to construct and were not as durable as a wooden board.
Statement of Significance
This object represents the constancy of the making and use of siapo among the Samoan people. The materials, designs, and applications have remained largely unchanged for centuries. Simultaneously, this object represents change, because this work was produced with a stitched ‘upeti, rather than a carved wooden one. The stitched ‘upeti was the old way of doing things, and the decline of their use is directly tied to more frequent interactions with outside markets and the rise in use of steel tools, such as carving. There are simultaneous truths manifest within this object. Though identical in material composition, it is separated from its modern counterparts by the creation of its design. It is a testament to the adaptations that are often made to make the continuation of traditional craft a practical endeavor.
Condition and Description
Overall, the siapo is in poor structural condition with significant creases, tears, and losses. It is in poor aesthetic condition due to abrasions and losses in the design, as well as overall surface grime. The cloth is rectangular in shape with approximate dimensions of just over 3 feet by almost 7 feet. All four edges of the cloth appear sharp, indicating that this section was likely cut from a larger piece. Additionally, the pattern on the cloth appears to have been truncated by these cuts, with design continuing beyond the sharp edges. These dimensions support the attribution of this cloth as a lavalava, or wrap-around-skirt. There are seven creases that run the width of the cloth, and two that run the length. These are likely to prolonged folded storage within a museum setting. Significant losses have occurred along these creases and the edges of the piece. Additional small losses have occurred in areas of dark brown staining and as result of possible pest activity.
The cloth is constructed using hand-beaten strips of bast fiber from the inner bark of the mulberry tree. These strips, no larger than 12 by 40 inches, are layered in two sheets with perpendicular grain direction. The ochre decoration of this cloth was completed using a rubbing method on a hand-sewn ‘upeti, or board, made from plant fibers and leaves. The use of hand-sewn ‘upeti leaves a positive impression of the designs crafted on the board. The board likely measured approximately 27 3/16 inches x 15 ½ inches - the dimensions of the repeating pattern.
Overall, the siapo is flexible. However, tape repairs applied to the verso has resulted in areas of stiffness. Four types of tape have been applied: a small masking tape label with an inscription, fabric tape that runs along both short sides, and packing tape located in four discrete areas on the verso. The masking tape and fabric tape are both brittle and have therefore lost some of their adhesion to the barkcloth. The pressure sensitive packing tape appears to be in the oxidation stage of deterioration, resulting in a tacky, stringy adhesive.
Treatment Summary

Surface Cleaning
The recto was vacuumed with a HEPA filter on low suction overall through a screen followed by two passes through Vellux. The verso was cleaned similarly but with one pass through Vellux.

Tape Removal
The packaging tape carriers were lifted from the siapo using a heated spatula set approximately to 130 degrees F. These carriers left residues behind which were temporarily covered with silicone release Melinex.
Future Treatment Steps
One semester was not sufficient time to finish the treatment of this object. Below are a generalized version of the remaining treatment steps outlined in our proposal.
-
Finish tape carrier removal
-
Reduce residues left behind from tapes
-
Humidify the object through Gore-tex
-
Flatten the object under felts and plexiglass
-
Mend long tears and compensate for losses larger than half an inch
-
Design and create appropriate storage housing
-
Carry out post-treatment documentation and photography